Within industrial processes and material management, the significance of high-performance granulators and heavy-duty shredders cannot be overstated. GM Diagnostics rely on efficient material granulation and heavy-duty shredding solutions to streamline their operations. Ultimately this ensures optimal productivity and waste management.
GM Diagnostics would like to highlight the safety measures associated with industrial granulator machines and shredders. Specifically, we wish to emphasise the ...
More
Bolton Engineering company talks about shredders and granulator solutions 2024
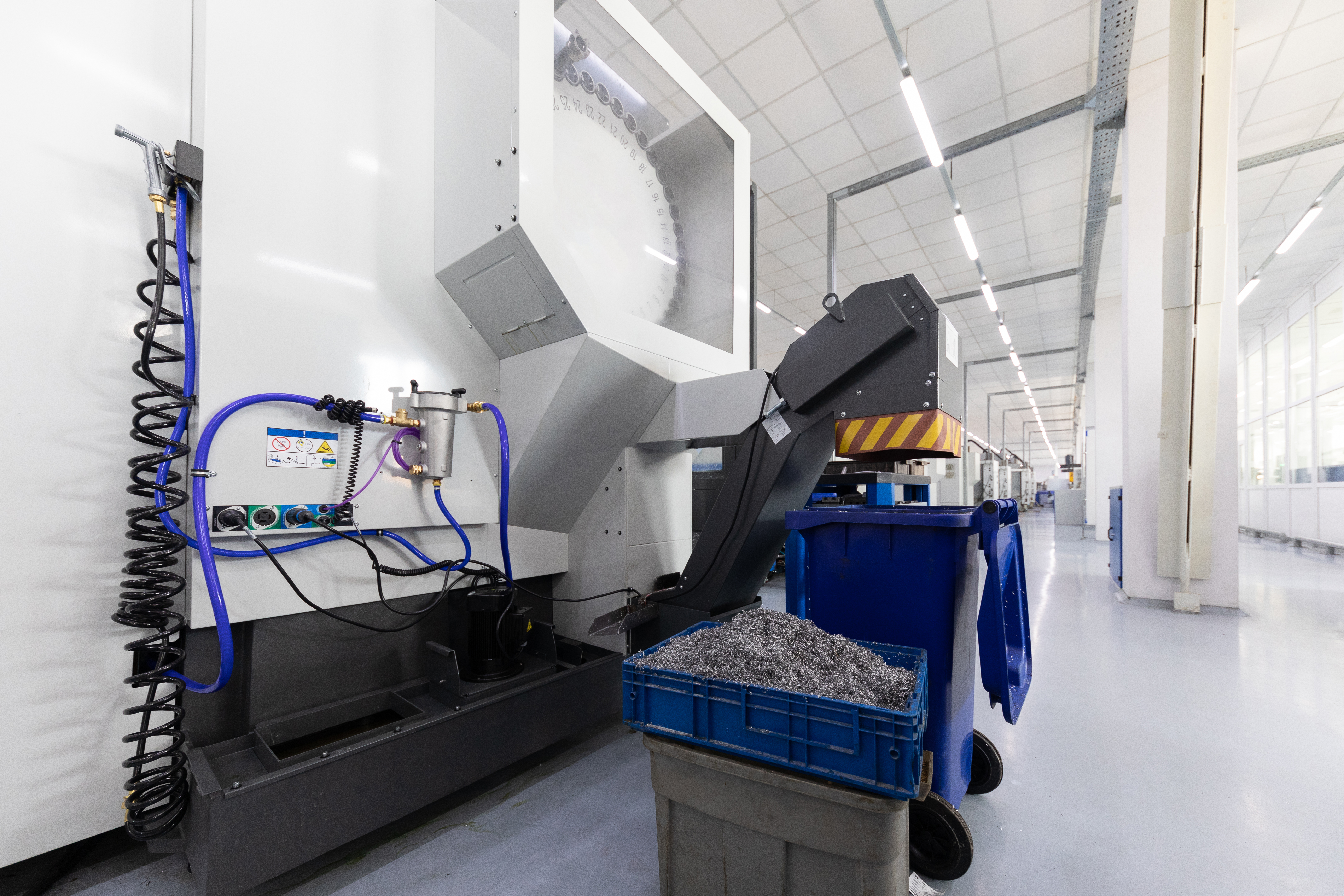
In the dynamic landscape of recycling, post-consumer recycling has emerged as one of the fastest-growing markets. This is fuelled by the scarcity of resources and rising energy costs. GM Diagnostics an established Bolton Engineering Company recognises the need for sustainable Shredders and Granulator Solutions, so we play a pivotal role in this sector.
Above all, this market thrives on repurposing daily waste into new products. Such as the transformation of PET bottles into yarns and fi...
More
Season’s Greetings from GM Diagnostics Engineering Services

As we reflect on another successful year at GM Diagnostics Engineering Services, we extend our warmest wishes and Seasons Greetings for a joyful Christmas and a prosperous New Year to all of you. Moreover, your unwavering support has driven our accomplishments, and we express our sincere gratitude.
A Year in Review: Achievements, Gratitude and Seasons Greetings
Indeed, throughout the year, our team of multi-skilled engineers has delivered exceptional services, contributing ...
More
A Comprehensive Guide for Injection Moulding Engineers
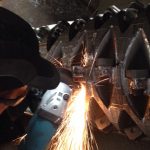
A Guide for Engineers in Injection Moulding: In the dynamic manufacturing landscape, injection moulding is a versatile and efficient process for producing complex plastic parts. Importantly, injection moulding engineers play a pivotal role in this realm, contributing to the design and production of high-quality components. In this blog, we delve into three crucial aspects of injection moulding: Design Guidelines, Technological Advancements, and Environmental Sustainability.
...
More
Understanding Injection Moulding
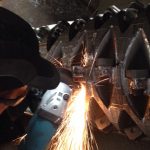
A guide to Understanding Injection Moulding in the manufacturing world, Injection Moulding is a versatile and widely used process for producing intricate and complex parts with high precision. From automotive components to household items, injection moulding applications are vast, making it a cornerstone of modern manufacturing. In this blog post, we'll delve into the depths of injection moulding, exploring its intricacies, common defects, and the diverse materials that bring designs to li...
More
Overcoming Challenges Faced by an Injection Moulding Engineer
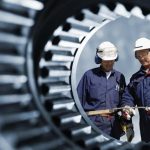
An Injection Moulding Engineer plays such a crucial role in the plastic manufacturing industry. In fact, they oversee the intricate process of creating various plastic components. However, they encounter several challenges during their work that can impact product quality, efficiency, and cost-effectiveness.
Choosing the right plastic material is crucial for successful injection moulding. Engineers at GM Diagnostics are responsible for material selection based on the specific requirements of ...
More
Sustainable Manufacturing with Eco-Friendly Granulator Blades
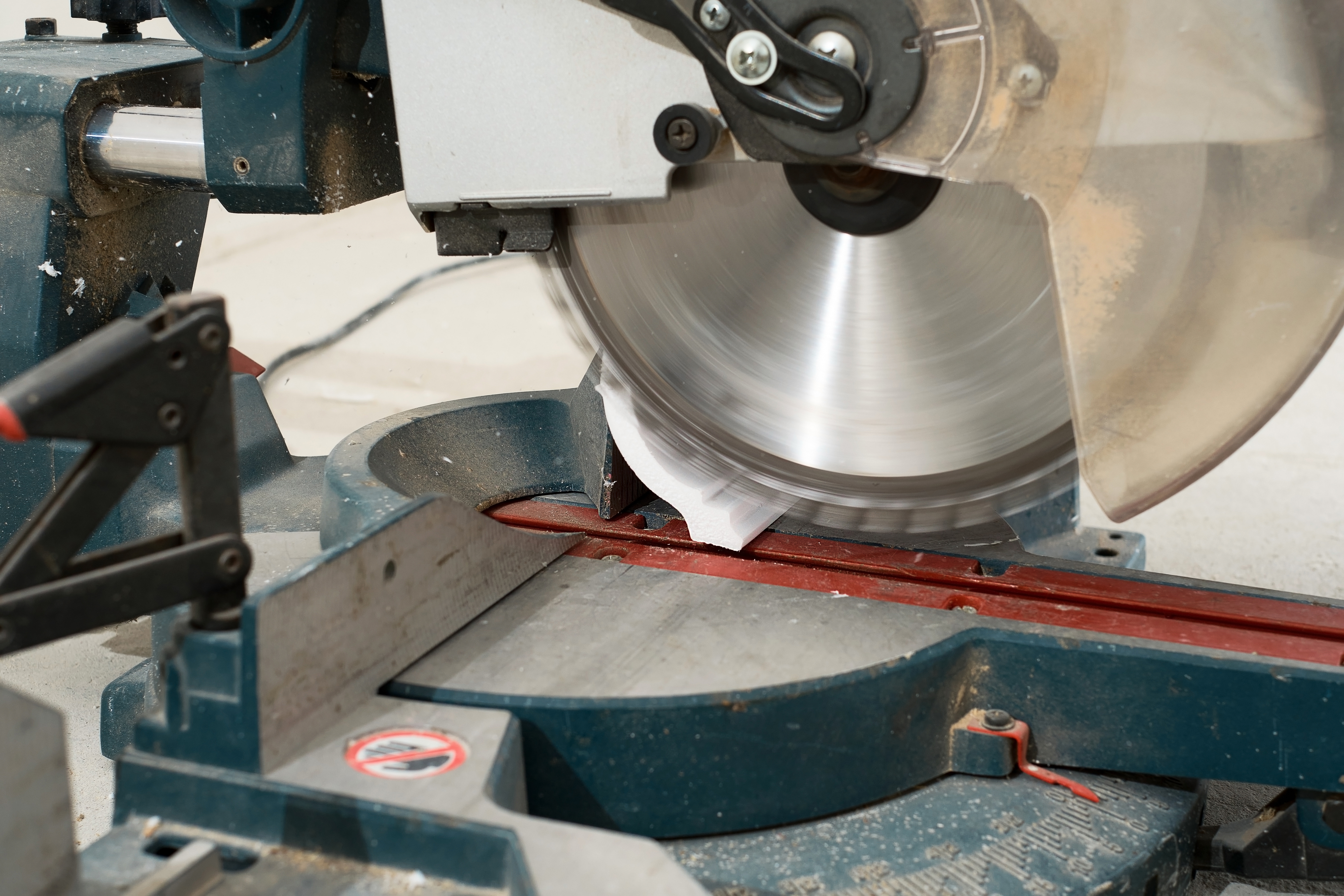
In an era marked by heightened environmental awareness and a growing commitment to sustainable practices, industries across the globe are reevaluating their manufacturing processes. This certainly includes GM Diagnostics, in particularly the increased demand for Eco-Friendly Granulator Blades services.
The shift towards sustainable manufacturing is transforming the way products are made. Above all, this is driven by concerns about resource depletion and environmental impact.
In this contex...
More
Engineering Companies Role in CO2 Emission Offsetting

In the face of escalating climate change concerns, businesses worldwide are under mounting pressure to reduce their carbon footprint and transition towards more sustainable practices. As the urgency to address climate issues intensifies, engineering companies play a pivotal role in supporting other businesses to offset their carbon emissions.
By leveraging their expertise, resources, and innovative solutions, engineering firms can help companies implement sustainable strategies and achieve th...
More
Granulator Blades

Granulators play a vital role in the recycling and plastics industry. Therefore, their efficiency heavily relies on the condition of their blades. Granulator Blades, also known as granulator knives. These essential components directly impact the quality and consistency of granulated materials. At General Maintenance & Diagnostics Ltd, we understand the significance of well-maintained granulator blades for optimal performance.
Understanding Granulator Blades
...
More
Merry Christmas & Happy New Year
With the year quickly drawing to an end, GM Diagnostics want to take a moment to show our appreciation to customers. We want to say a huge thank you to all of the customers this year and a Merry Christmas. Entrusting us to carry out technical services and maintenance on your machinery has been a privilege.
With many faults being overcome and many solutions being found, it’s now time to enjoy the festive period. As the New Year period passes, we will certainly be back to operating as usual. Ho...
More
How we can help with Maintaining & Repairing Heavy Machinery
Maintenance and Repairs only cross customers’ minds when the damage has already been done. So avoid being part of the majority and look into Maintaining & Repairing Heavy Machinery before purchase. Perhaps you may just get extra years out of machinery by knowing how to examine your machinery.
Each Machine will be different, however, leave the fault fixing to the General Maintenance & Diagnostics team. GM Diagnostics are Greater Manchester’s most reliable problem solvers when it comes ...
More
Milling Machine Repairs in Bolton and Surrounding Areas
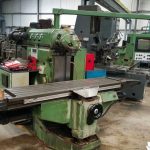
No matter their purpose or function, Milling Machines will be an essential way of intricate manufacturing. However, with the level of precision and just how effective they are any breakdowns need a swift solution. Above all, this is the reason GM Diagnostics carry out Milling Machine Repairs and similar services.
As well as specifically milling machines, we also cover most kinds of drilling machines. Each machine is different hence why we tailor each service specifically for your product. In ...
More
There is no better time for CNC Maintenance
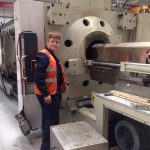
CNC Machines are massively important to modern day manufacturing, offering levels of precision not previously possible. Thus, if a CNC Machine begins to breakdown or slowly becomes faulty then you realise action should have been taken sooner. So, don’t wait until it’s too late and call GM Diagnostics for your CNC Maintenance services.
Maintenance can mean a lot of things, and with GM Diagnostics the choice is on you. Under maintenance includes draining, cleaning, performance measuring, potent...
More
Why you need Machine Tool Repair Services right now!
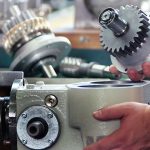
It doesn’t matter how well-put together your machinery is, machine tool damage can ruin the whole manufacturing process. Even with just one step of the process, this can completely derail the operation especially with precision manufacturing. Most importantly this doesn’t apply to just a couple of machines, so consider Machine Tool Repair Services now!
Slight bits of damage can be easy to put off or even try to fix yourself, thus don’t ever compromise. So, have you considered investing in eff...
More
Engineering company based in Bolton

General Maintenance Diagnostics Ltd, is an engineering company based in Bolton, North West, which has many years of experience and knowledge in engineering. We offer our customers a wide range of engineering services and support. Along with dealing with issues no matter whether it's machine or site related.
Although our Bolton engineers specialise in the plastics manufacturing and recycling industry, we offer our services to an ever-increasing array of industries. In addition to this, we are ...
More
Bolton engineering company specialise safe machine repairs
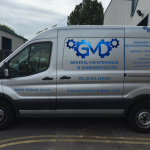
General Maintenance & Diagnostics Ltd, is an engineering company based in Bolton, North West, which has many years of experience and knowledge in engineering. We offer our customers a wide range of engineering services and support. Along with dealing with issues no matter whether it's machine or site related.
Although our Bolton engineers specialise in the plastics manufacturing and recycling industry. We offer our services to an ever-increasing array of industries. In addition to this, w...
More
Why its important to have the correct Material Blower Fan
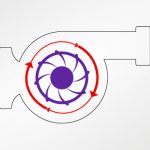
A Material Blower Fan (Centrifugal Fans) has a really important function, so it is important that you choose the right one. When shopping around for ventilation or cooling systems, it’s all about the right fit, not the most expensive option. Not only do these come with expectations but you don’t want to be overhauling your entire system for a fan.
Many Blower Fans, within a space of years, become dirty, rusty, and inevitably damaged after just a few years. This will most commonly be down to t...
More
A Guide to Granulator Screens and Shredder Screens
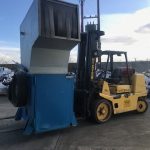
With Granulators there are plenty of things you need to know, even with just the screens. For those who don’t know: a Granulator is a machine which prepares old material for the new. The process of Granulating consists of grinding down and melting scrap material so it can be reprocessed.
Granulator Screens and Shredder Screens play a huge role in the performance of the machine. Whilst there are many different models from different brands, GM Diagnostics can make this easier. This is due to ho...
More
North West Engineering Company
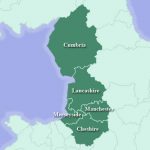
You always know someone who needs a North West engineering company to solve their machinery worries. So, instead of recommending they google it! recommend them the best for the job #GM Diagnostics.
GM Diagnostics is a Bolton-based engineering company, operating across the North West and provides repairs and services.
Fortunately for you, our machine engineers do it all! Our most popular services, for instance: installations and industrial machinery servicing, allow customers to make the mo...
More
Engineering Company for 2022 Machine Tool Companies
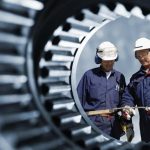
Is it time to refresh your old machinery? Whether you need a care package or a new product installed, this engineering company understands the stress this can cause. Thus, our team of engineers offers excellent services installing, maintaining, and repairing, everything from Material Blower Fans to Shredder Screens.
Being a North West multi-skills engineering company, GM Diagnostics engineering company works with a lot of different types of machines and tools on a daily basis. And, our Bolton...
More
Improving sustainability in manufacturing
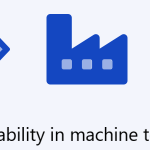
The amount of waste used up in Industrial Processes, such as Machine Tool Manufacturing, every year is extortionate. So, it is time to start improving sustainability in machine tool manufacturing by making machine maintenance services and manufacturing kinder to the environment. GM Diagnostics, industrial machinery repairs & servicing specialists, are here to inform you about how to make manufacturing more sustainable.
Even if you are searching putting industrial machine repair near...
More
A Happy 2022 from GM Diagnostics
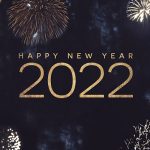
As we rapidly approach the New Year, GM Diagnostics would just like to wish all of our customers a Happy New Year! After a year full of COVID frustration, it is now time to put your feet up and look forward to the joys of 2022. With this being said, the whole team here at GM Diagnostics would like to thank everyone for their cooperation and patience throughout the past 12 months, and look forward to getting back to repairing and servicing machinery across the North West and beyond.
North West E...
More
Merry Christmas from GM Diagnostics engineering services
After another great year here at GM Diagnostics engineering services, we would like to wish everyone a very Merry Christmas and a prosperous new year. We would like to say a massive thank you to all those who have supported us this past year.
Engineering services we provide
As a team of multi-skills engineers, we offer a wide range of services covering most aspects of machine repairs and servicing offering support to the plastics manufacturing and recycling industries.
Our team are all Safe...
More
What can go wrong if your granulator isn’t maintained correctly
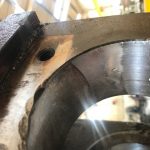
Your granulator is a massive piece of equipment that is incredibly hard working. And the last thing you want is for it to breakdown in the middle of the day and bring your working day to a complete stop. One easy way to avoid costly granulator repairs is to ensure that you have regular granulator maintenance booked in.
If you don't currently have a maintenance plan set in place, you might find that your machine could be suffering from any of these three issues -
Increased h...
More
Keeping your granulator blades in check
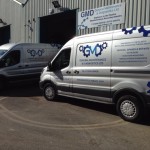
Keeping your granulator blades in check: Your granulator blades play a crucial role in the efficiency and productivity of your granulator machine. Therefore, proper care and maintenance are essential to ensure these hardworking components perform optimally. As a result, this guide will address common questions about granulator blades and offer insights into effective maintenance practices.
The Impact of Dull Blades
Granulator blades, when dulled, can result in a cascade o...
More
We have a new member of the team!

New Member of the Team
Everyone here at GMD are pleased to welcome Mark Walker to the engineering team. Mark brings with him a vast amount of hands on experience. With a history in maintenance and repairs of heavy agricultural machinery it won’t take him long to get a grips with anything we throw at him. Welcome aboard Mark.
More
Choosing the Right Granulator for your Business
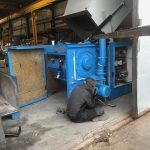
When choosing the Right Granulator for your Business, finding the perfect fit for your business involves carefully considering various factors. Due to this, there isn't a one-size-fits-all solution in the realm of granulating machinery, as each company has unique requirements and needs specialised equipment. As a result, at General Maintenance and Diagnostics (GM Diagnostics), we prioritise helping you select the most suitable granulator and machinery for your specific production needs.
 ...
More
How to reduce your plastic injection moulding costs

Injection moulding is a very effective way to mass product parts. However, there can be a huge amount of waste that comes with it. This waste can come from user error, down time, machinery errors and damage, and more. Here at GM Diagnostics, we carry out maintenance Bolton on a range of industrial machinery, including injection moulding machines. We've put together a few ways in which you can reduce the amount of waste and costs that might come with plastic injection moulding.
Injection M...
More
Which material will you choose for your compressed air piping?

When was the last time you thought about your compressed air piping system? For many companies, it's one of those things that is out of sight, out of mind. But in order to keep your compressed air and piping system operating as effectively as possible, you need to choose the right material for your business needs.
Here at GM Diagnostics, we're a Bolton engineering company with years of experience when it comes to pipe fitting and maintenance. that's why we have decided to write a quick ...
More
Injection moulding principles that need to be followed
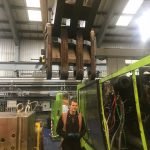
Working at the fore front of the plastics industry we see a lot of the positives and negatives that come with injection moulding process. One of the biggest negatives we have been noticing is that even though it is an extremely industry and these processes are used everywhere, there seems to be a huge drop in the standard of training and personal development.
Here at GM Diag, we have been carrying out maintenance Bolton and working with the injection moulding machines for years. Over th...
More
The benefits that come with a machinery maintenance plan
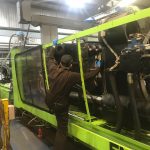
With the large machinery our engineers see and work on on a daily basis, we also see how many issues flare up with one of these machines break down unexpectedly. Not only will it cause a stop in work, it can also mean you have to spend time and money that you weren't expecting too, to get it fixed. Now we're not saying that a maintenance plan will completely stop any unexpected breakdowns, but they massively reduce the chances. Here are some of the main benefits that come with a maintenance plan...
More
Why book our Bolton engineers to visit you on site?

Our Bolton engineers spend the majority of their time out on other sites working on a range of different machinery. Over the years we have realised that it makes more sense to send engineers out to jobs than bring the jobs to the engineers. Especially when it comes to machinery that weighs over a tonne! But if you're still not sure why to consider on site machinery repair here are some of the main advantages that come with it.
On Site Bolton Engineers
The one of the advantages that...
More
Injection Moulding and the Basics
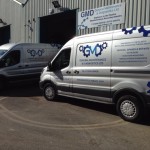
Here at General Maintenance & Diagnostics, we take pride in our collaborative efforts across various industries, providing crucial engineering and technical support to businesses in Bolton and extending our services to clients further afield. Our dedicated engineers are stationed in warehouses, offering valuable assistance to teams engaged in diverse sectors, such as manufacturing and recycling.
Among the myriad machines our skilled Bolton engineers frequently encounte...
More
Engel clamp rebuild
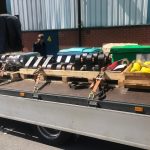
The GM Diagnostics team were asked to take a look at an issue with a 600t Engel injection moulding machine. After a couple of attempts to resolve an issue with the clamp by other companies, we were asked to get involved.
Our engineers carried out a full strip down of the complete toggle system and that revealed several broken toggle pins and extensive wear to all links and bushes. The customer had been quoted a 16 week lead time to repair and in excess of £70,000.00
However we were able to...
More
Improving an injection moulding machine’s cooling system
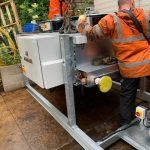
Improving an injection moulding machine's cooling system is crucial for achieving efficient and high-quality production. Recently, a new customer approached us with a faulty injection moulding machine cooling system. Once we examined the machine, it was obvious to GM Diagnostics that the system in place needed to be replaced.
Their current cooling system was plagued with leaks and a massive reduction in flow rate down time was an issue. In general, the cooling system plays a vital role i...
More
We fix your machines in a time scale that suits you!
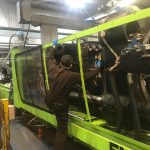
Our Maintenance Engineers in Bolton have been working on dismantling full toggle link and toggle pins from a Engel 750 (as seen in the image below.) Most of the wear was found along one toggle pin which had seized and cracked in several places. Lead time from the machine supplier to repair this was 12 weeks and GMD estimate a full rebuild within 4 weeks at a fraction of the cost.
After the removal of two tie bars, the whole of the toggle system had to be stripped out of this 7...
More
Further investment at General Maintenance & Diagnostics LTD!

We are very proud of the work we carry out in our machine shop based in Bolton Lancashire, and all of our employees work hard on everything they do. As a company, we try and do everything we can to make their jobs easier and that is why we have decided to invest in a third Granulator Blade Sharpening machine.
This machine will go along side our two existing machines, which means we know have two 3.1 meter machines and one 2.1 meter machine. Our additional machine is being delivered ...
More
Our Bolton based machine diagnostic services
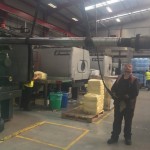
Here at GM Diagnostics, we have a team of multi skilled engineers, who are able to offer a wide range of services covering most aspects of maintenance Bolton, machine repairs and servicing offering support to the plastic manufacturing and recycling industries.
Maintenance Bolton
We have a large warehouse based in Bolton. Our warehouse has been purposely adapted to allow our engineers to bring in large machinery and safely work on it. If, for any reason your machinery can't be removed then our ...
More
We have taken over the service, spares and parts of Birmingham Granulators LTD
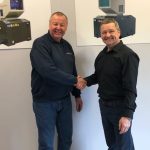
We are happy that we can now announce that GMD have purchased the ongoing business activities of Tamworth based Birmingham Granulators Ltd.
The business name Birmingham Granulators Ltd will be retained by Tim Aaronricks who will now focus on second hand machine sales, special projects and consultancy work. Here at GMD we will focus on what we do best which will be the service and installation work, blade changes, in house blade sharpening and spare parts.
New partnerships for GM Diag&nbs...
More
GM Diagnostics – What can we do for you?
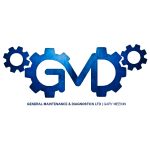
At GM Diagnostics, our Bolton-based engineering company has firmly established itself as a key player in plastic manufacturing and recycling. Over the years, our expertise has expanded to encompass various industries, reflecting our commitment to versatility and excellence in engineering solutions.
Our Core Services:
Our extensive workshop facility is at the heart of our operations, equipped with state-of-the-art tools and manned by a team of skilled professionals. We tak...
More